What does it take to strip down, overhaul and reassemble, one of the world’s most dashing fighter? It takes hundreds of professionals, expertise, precision and intuition, pushing everyone to the limit. At the MRF, the major overhaul of Mirage is performed utilizing specified tools and even cleaning is a specialized job. Once the Mirage is dismantled and de-painted, the teams check the airplane structure for damage right down to the last screw. At the same time engineers perform any repairs needed on the wings, landing gears, flaps and engine. It’s not like a Microsoft package off the shelf. It’s like an aircraft model kit with different parts made across nine different establishments, all under the umbrella of the MRF.
Dassault Mirage is one of the most famous fighter jets of the air forces around the world – for pursuit, attack and reconnaissance. It can fly at double the speed of sound and is renowned for high levels of reliability and versatility. In PAF, the Mirage has always been considered the backbone for decades. However, every ten years, at the very least, or after 2,000 flying hours, every Mirage has to clear its schedule for an important job – a Grand Visit (GV) or a complete overhaul. It all starts with ferrying the Mirages to the Mirage Rebuilt Factory (MRF), expert at jet maintenance and overhauling. During this time, engineers dismantle the entire fighter jet and specialists check the ejection seat, the skin and perform engine checks. All of this in nine months, at the MRF PAC Kamra, less than an hour drive from Islamabad.
How it All Started
PAF made a contract to induct Mirage aircraft in 1967. The first ferry flight of six aircraft under the leadership of legendary Air Cdre MM Alam (then a Wg Cdr) arrived from France to Pakistan on 8 Mar 1968. While the initial arrangements for F-6 overhauling had started to take shape, the need was also felt to establish a similar facility for the newly inducted Mirages. The overhaul cost of the Mirage aircraft from France was exorbitant and the process was time consuming. In 1975, the first aircraft became due for overhaul in France, at a cost of $1 million per airframe and $0.17 million for each of its engines. With overhaul dates of Mirage fleet approaching fast and the astronomical expenditures associated with overhauls from France, efforts to establish an in-country overhaul facility for the PAF Mirages were initiated in 1974, under ‘Project-741’. It was subsequently shaped into the Mirage Rebuild Factory.
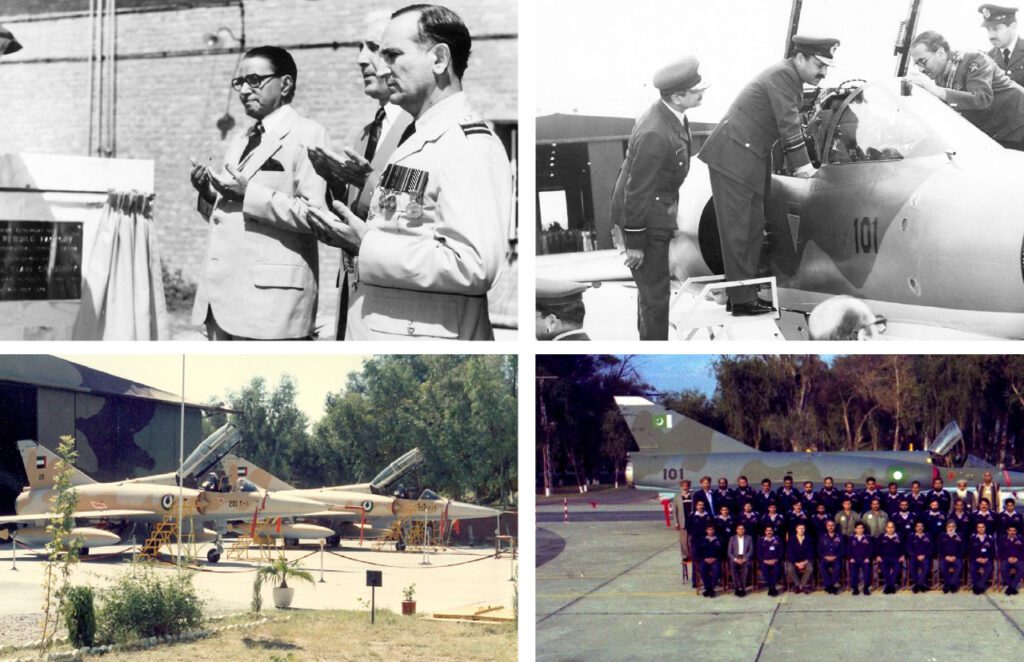
Wg Cdr GM Siddiqui, who was appointed as first director, MRF, Kamra, recommended a suitable site, where the F-6 facilities were already under construction. In 1975, under its first Director General, Air Cdre SM Saeed, the establishment became the first factory to start production in 1978, and accomplished complete domestic overhaul of the first Mirage jet in February, 1980. The initiative gave the PAF the added advantage of achieving a nucleus of training manpower for future undertakings. Since then, the MRF never faltered in keeping the PAF’s fleet in the best possible shape. In fact, the aircraft and engine overhaul capabilities available at the MRF remained a source of reassurance, which encouraged the PAF to acquire used Mirages from all available sources in the world.
The MRF presently comprises nine wings, one each for the overhaul of aircraft, engine, components and accessories. The factory was also being readied to overhaul the F-16 engines, and to expand its manufacturing facilities to make parts for the airframes and engines of all fighters and trainers in the PAF inventory as well as those of some friendly countries.
The first package of the Australian Mirages, consisting a sizable number of aircraft, components, spares and engines, was acquired in 1990. These planes were overhauled and brought into service, adding two squadrons to the Mirage fleet of the PAF. In 2000, used Mirage IIIs were acquired from Lebanon. They were also overhauled and brought into service, enhancing the strength of the PAF’s Mirage fleet. Some of the Libyan Mirage V, inducted in 2004, were made air-worthy and the remaining reduced to spares.
Nine Months Cycle
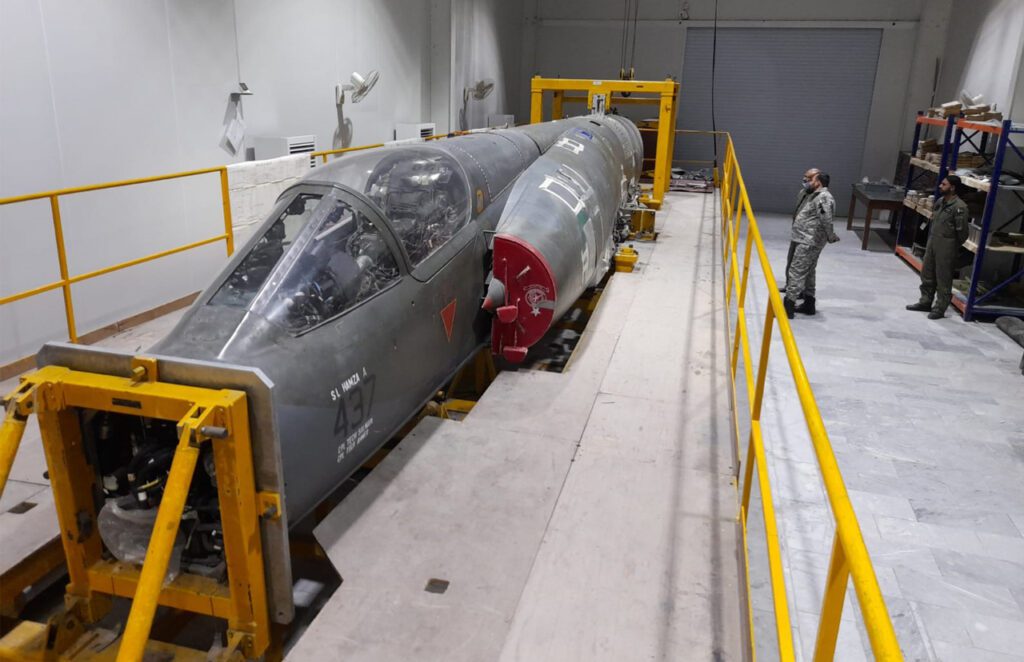
After the aircraft has arrived at the MRF from the flying squadron, the first job is to put it in the hanger at an assigned dock. The airplanes are lifted on jacks, similar to ones you have in cars, only much bigger later, a team of engineers and technicians under the leadership of Gp Capt Najamul Hasnain, Chief Engineer at MRF, carries out the initial inspections in minutest of details. “Once we strip down the plane, we kick into the inspection mode,” Najamul Hasnain said, while talking to the team of ‘Second to None’ that visited the facility in January this year. In nine months, the jets have to be ready for take-off and return to its squadron. Different teams work simultaneously on every part of the plane. All of them work in sync, which is why they depend on each other. Its like a well coordinated team work where every member knows its responsibilities and importance of meeting the desired timelines.
On the disassembly line, 12 Mirage jets can be docked, where they were seen in different phases of disassembly and build-up. The Mirage V PA2 from No 8 Sqn, had clocked more than 2, 000 flying hours and it was time for a mega pit stop. At Dock No 2, it had been taken apart and looked quite different than we might imagine. It was on its grandest visit, as the ground crews called it, or GV-III, its third overhaul after 32 years of service. The abbreviation ‘GV’ stands for a French word ‘Grande Visite’, that involves major inspection and overhaul of the Mirage aircraft. The entire PAF Mirage fleet has undergone two overhaul cycles of GV-I and GV-II at the MRF.
Need for GVs
The complete Mirage has been the backbone of PAF strike force since long. The nation witnessed it’s capabilities, recently, in Feb 2019 during Ops Swift Retort. First of all, I want to acknowledge and pay tribute to the services rendered by our pioneering team of officers, airmen and civilians who, over decades, have worked tirelessly in keeping this weapon system up in the skies,” said Air Cdre Saquib Niazi, who is the Managing Director (MD) Mirage Rebuild Factory (MRF).
Air Cdre Saquib Niazi, said that Pakistan was the only country where these versions of the Mirage had been retained in service beyond the lifespan of GV-II. The PAF needed its Mirage fleet to fly for some more time. Being the center of sustenance for the PAF Mirages, the MRF was once again entrusted with the task to find a solution. After carrying out a thorough feasibility study, in consultation with the manufacturer, the MRF devised a new inspection package by the name of GV-III. Later, two Mirage aircraft were subjected to GV-III inspection in January, 2005. As the these Mirages were undergoing GV-III, there was a change in the plan.
“With the expected phase out of the Mirage fleet in the near future, the PAF needed a maintenance package that could keep the Mirage fleet operational. A revised maintenance package named ‘Mini GV’ was implemented in consultation with the Original Equipment Manufacturer (OEM). It provided almost half the lease of life compared to GV-III,” Air Cdre Saquib Niazi said. The senior official explained that pre-empting the inevitable shift in the phase out of the Mirage fleet, the MRF also conducted a detailed study to enhance the fleet’s life beyond the year 2020. “A new concept of the Delta-GV was introduced, which had been implemented since 2012, after consultation with the OEM,” MD MRF elaborated.
“At the MRF, we overhaul 550 plus components, fuel pump, hydraulic and fuel systems, engine parts in the various variants of the Mirage possessed by the PAF. In a year, MRF overhauls 4, 500 plus parts for the PAF. We are the OEM for the Pakistan Air Force,” the senior official said proudly.
Giving a New Look
Meanwhile back in the hanger, on Dock No 2, the Mirage which we saw earlier was all dismantled. Sqn Ldr Farazuddin Taimoori, Director Quality, MRF and his team had to finish this particular aircraft in the specified time so that it can return to the unit. This also meant a whole lot of time pressure. The team had gotten to work right away.
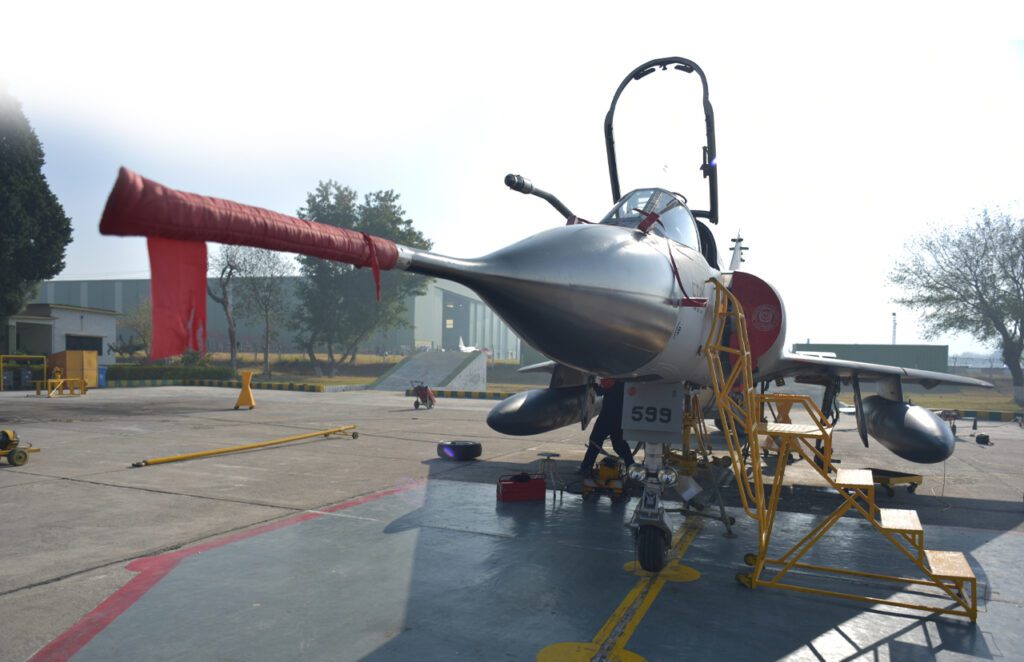
Back at the cleaning bay, it was almost like a car wash – a little more hardcore than removing squashed insects from the windshield. Mirages are a good 50 years old. Every single scratch has to be repaired. If they find larger damages, they even replace parts. The engine is removed first and later the aircraft de-painted to expose the structure for inspection. The Chief Engineer and his team scanned every inch of the plane with utmost precision. Engine parts were sent to the Component Overhaul Facility, which was established in the early 1980s, as a mandatory requirement for supporting aircraft overhaul. The Components Overhaul Facility has continued to go through the modernization process. The setup has acquired the capability to overhaul and produce more than 10, 000 Mirage components every year. Lately, the JF-17 related testers have also been added to the facility.
Later, the wings of the aircraft are dismantled and sent to the Wing Refurbishing Facility at the MRF. Since PAF operates different variants of the Mirage – Libyan, Australian, Lebanese, single and dual seaters etc, the team faced a huge challenge of keeping the window for maintenance work and overhaul as small as possible. Everyone at MRF knows that they are the sole facility for Mirage overhaul and PAF leadership has trust in the capabilities of the personnel. With this honour, come the challenges of procurement and thus intensive indigenization by the PAF,” said Farazuddin Taimoori.
With the clock ticking, teams had also removed the outer shell and started looking for any damage. This involved undoing thousands of screws. “We are talking about very small parts here, which is why we need all the intuition and experience,” said Farazuddin Taimoori.
At the Engine Wing
All materials age. In the Engine Wing, the technicians examine the fighter jet’s power source, the ATAR engine.
Mechanics started screening the turbines, compressor and the afterburners, and that was no easy task. Over the period the men at MRF had gained mastery of overhauling the robust ATAR engine of Mirage. Like the airframe of the aircraft, the ATAR engine is also stripped down to individual components. All components undergo a thorough cleaning process to remove the contaminants accumulated during the flights. The cleaning process helps in identifying the defects present on the jet engine parts. The cleaned parts undergo non-destructive inspections to identify the existing defects. Specialized radiographic inspection techniques identify even the minutest cracks in the parts. The radiographic machine is equipped with a robotic arm to position the part for accurate identification of sub surface cracks.
Once all done, the newly overhauled engine is taken to Multi Engine Test Cell.
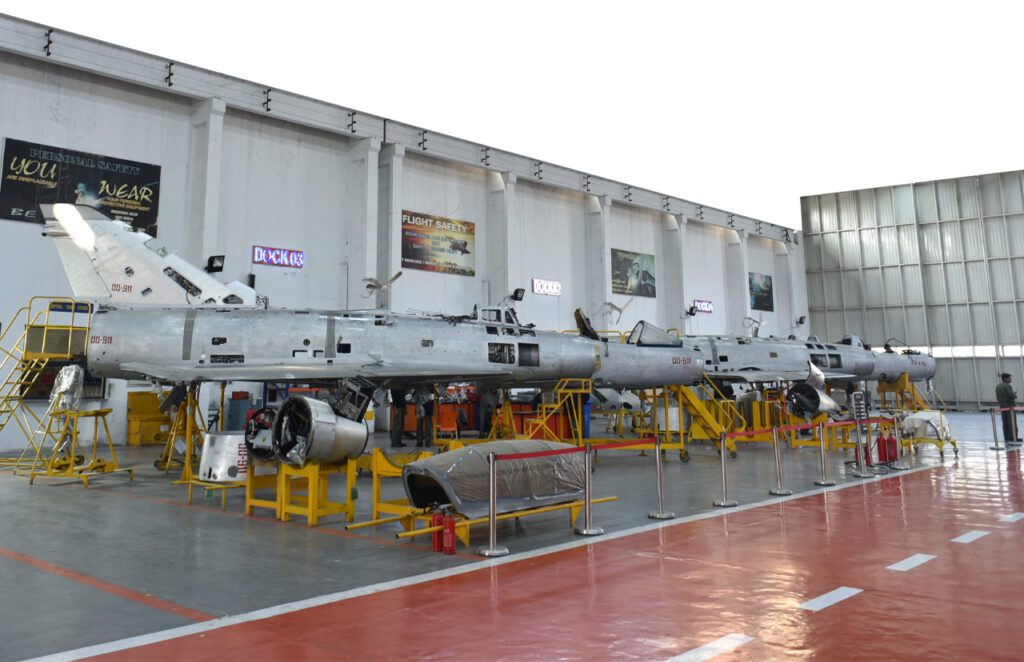
This facility is capable of test running F-100 and ATAR engines from idle to their maximum thrust in after burner settings.
As our trip down the disassembly and assembly line continued, we saw a few jets getting closer and closer to the final product, so complex than we could comprehend. On Dock 5, the Mirage III-EP came together like a giant puzzle. Ferried to the MRF last year, this aircraft was in the various stages of re-installment – being readied for rollout in specified time. Crews performed system adjustments on the aircraft. Structure, circuit and mechanical integrity checked and operated. “We can simulate the aircraft flying at 40, 000 at 700 knots,” said the Squadron Leader. “This is the point where minus the engine, the plane is 100 percent ready.” Another job ticked for the mega pit stop, but it was not the last.
In the Wing Refurbishing Facility, Wg Cdr Sarwar Imam of Structure Repair Wing, MRF, and his team checked deformities in the extensions. Sometimes it could take a year to repair a wing, and was more cumbersome than fixing the fuselage. In this hangar, the crews carried out refurbishment of wings as well as the fuselage. “At the moment we are repairing the fuselage of an aircraft extensively damaged after fire. Four out of its ten frames were damaged that seemed irreparable. But we are going to make it work. This jet will be ready in a short time. Damages to the jets could be caused by bird strikes, heavy landing, barrier engagement, and belly landing etc. “But damages caused by fires are to be rectified with precision,” Wg Cdr Sarwar Imam said.
Over the years the MRF had made 22 extensively damaged Mirages fully functional. They did not seem they could ever fly again, the Wg Cdr said. He also gave the example of the damaged SAAB aircraft, which had been declared beyond repair by the original equipment manufacturer (OEM) back in 2017-18. “But it was repaired by the Refurbishment Facility, which also carries out indigenous production of parts. The aircraft is back in the squadron and is fully operational now,” he said.
When, Wg Cdr Sarwar Imam and his team finished the wings, they pass it on to the next team. It really is just a big systematic process, with every single individual along the way adding their touch before passing it along to the next person along the line.
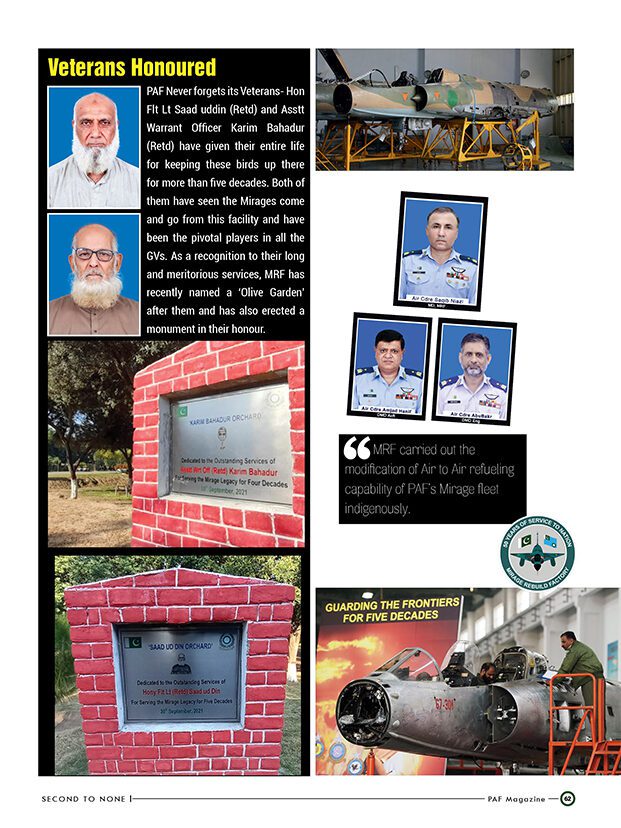
Honouring the Veterans
Meanwhile, once the engine had been installed, the aircraft has to undergo two taxi tests, before it was released for flying. The plane was also subjected to two Functional Check Flights (FCFs), in which the aircraft was pushed to the limits. This was followed by fuel checks for consumption during the flight. Mach runs were conducted at different altitudes, in which various systems were initiated to check their serviceability.
Then comes the Re-assembly phase. When the aircraft has gone through all the re-assembly phases, its time to take a ride. Outside, under the pleasant afternoon winter sun, Dock Chief, Asstt Wrt Off (AWO) Karim Bahadur, worked alongside a young team on the landing gear of a Mirage that was scheduled for a FCF mission. Recruited in December 1981, and after serving at Rafiqui, Karim Bahadur, came to MRF on March 2, 1985, where he specialized on the landing system. After retiring in 1999, as Dock Chief, PAF retained his services, given his expertise, especially to assist younger ground crews wherever they needed guidance, inspiration, and achieving precision. Karim Bahadur, is one of the oldest indispensable crew members that the PAF refused to let go of. There is an orchard of olive trees named after retired AWO Karim Bahadur, for serving the Mirage legacy for four decades, just like there is one dedicated for retired Honry Flt Lt Saaduddin, for 50 years of outstanding service. It is obvious that PAF never forgets its veterans and always honours them in a most befitting manner.
What’s rocket science to us is mammoth and complex work carried out at the MRF. Karim Bahadur, helped the PAF rebuild a Mirage, obtained from Australia, which was reduced to spares. “Imagine that it was just the fuselage, without the wings and fins. We collected its parts, put them all together and recovered this aircraft for the PAF. Karim Bahadur recalled he dedicated his career to rebuilding the Mirage. “The Mirage is my life,” he added.
Back to where it Belongs
Right next to the aircraft at the tarmac, stood proudly, Sqn Ldr Naveed from No 50 Sqn, who had just returned after performing a second taxi test and parked his jet, right in time for the Second to None team, to learn how well the engineers had done the job. Pilots are used to the aircraft responding immediately and maintenance errors are out of the question, that’s why specialists were testing the plane one last time. Climbing down from the cockpit, Sqn Ldr Naveed, performed a post flight inspection, checking for leaks, missing screws, engine condition. With a flashlight in his hands, he inspected the main hydraulic lines in the landing gear for leaks and checked for scratches“ has been completely overhauled and we need to ensure there are no leakages in the hydraulic lines. There are so many people thinking, designing and producing, so when we jump into the air, we feel confident as we have full faith in our ground crew,” said Sqn Ldr Naveed, who also agreed to give a joyride once the plane was ready and of course after permission from the top bosses. Major milestones cost the men hard work, concentration and sweat. It was a job very close to their hearts. If they made a mistake, it could cost someone’s life. Can’t afford to lose a friend or a colleague.
MRF – A Versatile Facility
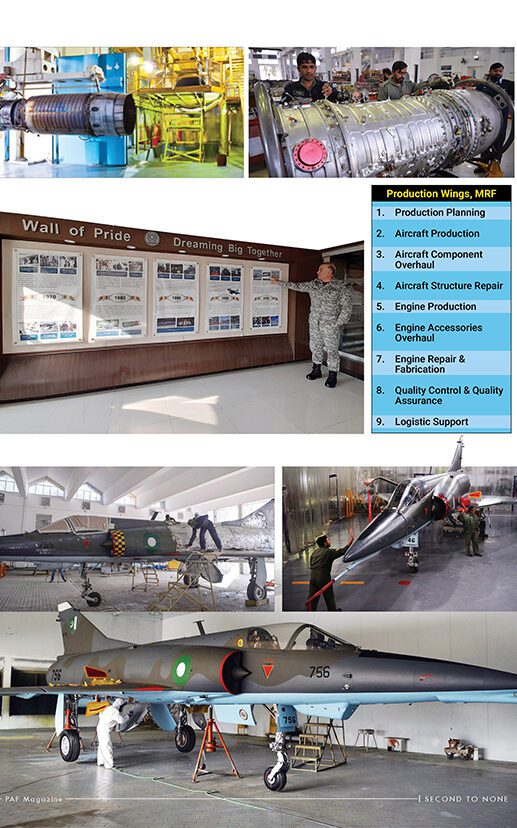
Today, the Mirage Rebuild Factory, is a dynamic setup that undertakes a variety of aircraft and engine overhauls. MRF is also responsible for structure repair of western platforms besides the other weapon systems of PAF. This also includes damage analysis and formulation of repair schemes. These capabilities were instrumental in the recovery of Saab aircraft.
MRF has pioneered aviation coatings for airborne platforms of PAF and its upgraded facility meets European aviation standards. MRF also upgraded PAF’s vintage aeroplanes with modern avionics suite along with weapon integration. Air to air refueling capability in Mirage aircraft was undertaken by acquiring state of art technologies by MRF. The facility is pursuing establishment of a repair facility for 4th generation helicopters. In this regard, PAC would become an approved supplier for Leonardo helicopter division and creation of a recognized maintenance center would serve as a regional hub for all types of scheduled inspections and depot level repairs. This includes overhauling of engines of Mirage, F-16, C-130, Karakoram-8 and T-37 aircraft. Mirage is an engineering masterpiece, precisely tooled against impossible odds, a real delight to fly, however, the nine-month process is complex and full of challenges. “It’s something which keeps you on the edge, always concentrated, a job that makes us feel proud,” said Air Cdre Saqib Niazi, MD MRF. “That’s all their hard work. Makes you proud to know that you’ve done a good job,” he added.
Nevertheless, the men can’t put their feet up yet. Further down the assembly line the wings and tail were being added to another jet. Finally, it looked like an aircraft. Means of take-off were added to another. This model was complete, and ready to be put to the ultimate tests. It’s butterflies when the plane takes off for everyone involved. For the Chief Engineer and Director Quality, their next project was already waiting in the wings. These crew members were the unsung heroes of the PAF, for building the Mirage for the most demanding of tasks, and transforming it into the guardian of safety under which millions of Pakistanis slept in peace.