The power of additive manufacturing cannot be denied as it has revolutionized the way manufacturing procedures are approached. For aerospace, additive manufacturing holds immense potential. From cost-cutting to enhanced performance, the possibilities are endless. The author invites you to take a sneak-peek at this emerging technology and its implications for the aviation industry.
The world of aerospace thrives on innovation and perpetual adaptation of new technologies. With such complicated processes and equipment, aviation engineers and pioneers are constantly on the lookout for new technologies. From supply in which contractors run out of business before their parts need replacement to manufacturing, which often requires tons of waste to produce a part weighing in kgs, aerospace industry is, by nature, an expensive business. That is precisely the reason why additive manufacturing seems like a godsent for the industry. Although, the technology is still in its adolescence, it offers massive advantages over traditional approaches even now. Let’s begin with understanding how the process of additive manufacturing, also called 3D printing, works.
A revolutionary approach to industrial production, additive manufacturing helps create products and parts which are lighter and stronger, with substantially increased efficiency. It is an apt example of another industry entering into the digital realm, rendering huge benefits. Additive manufacturing uses specialized 3D software known as CAD (Computer Aided Design) to precisely design objects which are to be 3D printed. Another method that is being used is 3D scanning, which has recently been developed enough to be operated even on small mobile devices.
The major difference in traditional and additive manufacturing is that in additive manufacturing construction material is added or laid down in layers through intricate processes to create an object. On the other hand, traditional approaches usually use subtraction or removal of excess material to create, using processes to mill, grind, carve, file, etc to reveal the required shape. Even this basic difference between the two approaches is enough to comprehend how additive manufacturing is significantly more efficient of the two.
How does it work?
Additive Manufacturing (AM) usually works by depositing layer upon layer of construction material to create a 3D, physical object. In a nutshell, each layer of material is laid upon the previous partially melted or melted layer of material, fusing them together. The object is first created using CAD, which creates the object in 3D, slicing it into ultra-thin layers. A nozzle or ‘print head’ deposits the layers of material, guided by the precise data given by the CAD. As the layers cool or are cured, the material fuses together, forming the end object.
Materials used in Additive Manufacturing
Various resources can be used to make material that is used in additive manufacturing. AM uses a diverse set of materials, ranging from complex metal alloys to chocolate. The most commonly used are Thermoplastics like Acrylonitrile butadiene styrene (ABS), polylactic acid (PLA) and polycarbonate (PC).
Metals ranging from precious metals like gold and silver to strategic metals like stainless steel and titanium.
Ceramics including zirconia, alumina and tricalcium phosphate.
Biochemicals are toughened material which can augment bone structures and growth. They can be created using silicon, calcium phosphate and zinc.
Researchers are currently experimenting with bio-inks made from stem cells to form various human parts, starting from blood vessels to bladders.
Additive Manufacturing in Aerospace
In 2018, General Electric completed a total of 30 thousand jet fuel nozzles by additive manufacturing. The nozzles were 25% lighter and 5 times more durable than their older counterparts. However, it turns out that GE underestimated one crucial benefit which made the nozzle a breakthrough piece of technology. The degree of combustion in jet engines determines its efficiency and these nozzles play a huge part in that process by evenly distributing fuel in the combustion chamber. The nozzles printed by GE had highly intricate veins that provide incredibly efficient fuel spraying. This reduces the engine’s fuel consumption by 15%, which is an impressive amount, all considering.
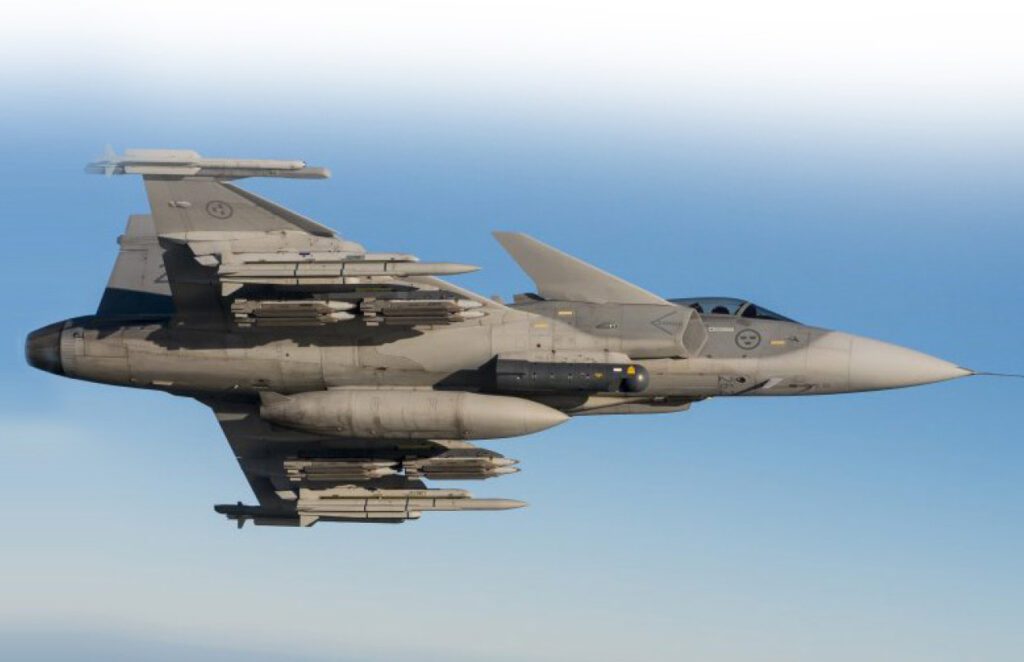
Let’s consider another case from USAF, that of a toilet that was to be fitted in a B-1 Lancer. The original toilet was to be replaced and a new one was to be designed, manufactured and fitted. For those who are confused about the fuss surrounding a toilet seat, it would be prudent to remind them that the toilet seat that was to be installed had to function impeccably at thousands of feet in the air, without there being any possibility of it rattling, leaking or malfunctioning. And all of this had to be done without revealing it to enemy radar. And on top of all of this, every single part and component needs to be approved, a process that can take months at a time. This sets the stage to elaborate how strange and complex of a niche aviation spare parts is. Parts and components are made to be tough and to last for decades. The same goes for aircraft and equipment. So, at times, when a decades-old aircraft requires a part, the original manufacturers are long gone. In these cases, the air force has to look for new contractors and manufacturers from the get go. Then, comes the long and tedious process of getting them through bidding, testing and security approvals.
Once approved, these manufacturers have to create the required parts using decades old drawings or reform decrepit moulds. Using conventional methods which include metal forming, casting, machining, and welding, the manufacturers need to have a specialized and highly trained array of equipment, human resources and capabilities. Even with these available, it takes a copious amount of time. And that is if the most effective approach to production is known. Otherwise, that needs to be figured out, as well. For example, the aforementioned nozzle from GE was unsuccessfully casted 8 times during its development phase owing to its intricate geometry.
Even post-delivery, the manufacturers have to wait for funds to be released, another process that takes extensive periods of time. That’s the reason working on small orders, even if the air force is promising a small fortune, is not everybody’s cup of tea. A statistic released by USAF claimed that through every single quarter, the military has about 10, 000 requests that go unanswered, despite the high pay-outs being offered.
Additive manufacturing can offer solutions or at least make things much significantly better with most of these problems. It can drastically cut down the time and resources needed to build aircraft components. Roughly every fifteen years, the global aviation fleet doubles in size. This puts tremendous pressure on manufacturers, having to consistently create new planes while keeping in line with new legislation. 3D printing can drastically reduce the time it takes to create plane parts, and will soon be the industry standard for manufacturing certain elements.
Most parts that are currently being 3D printed were previously either unavailable or had extensive waiting periods to acquire. Through additive manufacturing, the parts which usually take weeks, months or, in some cases even years to acquire using usual processes, can be printed within days. As the materials used to create the part are known and tested, there is no need to extensively test every material. Long, bureaucratic processes are also eliminated. A single 3D printer can easily manufacture specialized components which previously had to be made using several suppliers and contractors, each adding cost and time. As air forces print and formulate code for more and more parts, its library will grow and the cost of additive manufacturing will drop significantly. As an example, GE ran an experiment to print an old helicopter engine in 2017. They found out that just 6 engineers and a single 3D-printer could displace more than 10 – 15 full suppliers needed to prototype it with traditional methods.
Design
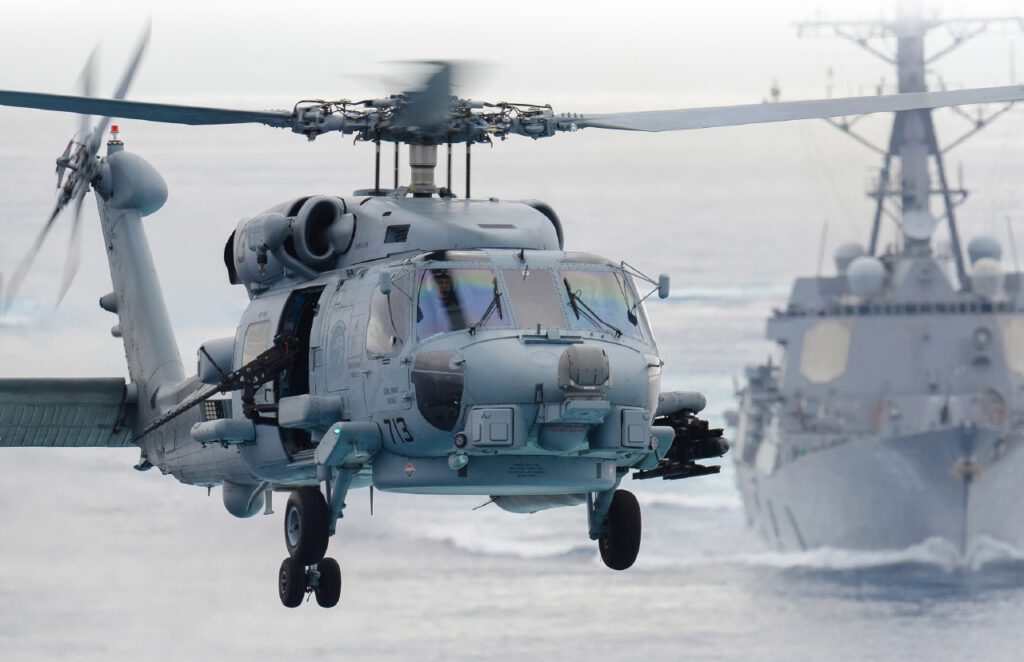
Aviation specialists agree that additive manufacturing has given the industry much-needed freedom when it comes to designing and prototyping. As opposed to conventional manufacturing, additive manufacturing uses specialized CAD software which gives the designer a new level of precision and the ability to leave the heavy chunk of technical aspects to the software. Designers can focus on the creation, solely. Moreover, with the approach that additive manufacturing utilizes, it has become possible to create complex shapes that were simply not possible through traditional metal fabrication. Additive manufacturing also offers creation using multi-materials, printing two different materials on either side. For example, aluminium on the outside and a more conductive metal on the inside. It even allows for increased ruggedness and durability in the design. A honeycomb lattice design is notoriously hard to create using conventional methods. However, with additive manufacturing a lightweight and sturdy honeycomb design is easily achieved.
The efficacy of this technique can be observed in Aurora Flight Sciences’ 3D printed aircraft. The ambitious project is a jet-powered, thrust vectoring, blended wing body aircraft which is remotely piloted. The construction of the jet has been completed using beyond surface geometry which has only now been made possible via additive printing. Aurora utilized ‘topology optimization’, an approach that dissects and duplicates structures found in nature. These structures shed excessive internal material for optimum, repetitive structures which offer substantial advantages over older techniques.
Assembly
Another benefit of using additive manufacturing is apparent in the assembly of parts and even aircraft. The wing being developed by NASA and MIT is the perfect example of this structure. A majority of aircraft wings in the future could be manufactured as one single part, instead of manufacturing several smaller components and putting them together. This technique can also be observed in a 3D printed heat exchanger for a catalyst, which is usually made from 300 different components but now can be made as a single part. Additionally, with the advancement of 3D printing using metals, different alloys and metals could be deposited in the part as required, making areas of the part tough, light and so on, making the aircraft much more functional.
Another vital change that additive printing can bring to the table is on-demand printing. Airbus is currently trying to develop 3D spare-part printing units in its storage areas. These storage areas already possess a few thousand parts each for accessible repair. Airbus is trying to equip the areas further with on-demand 3D printing which could potentially 3D print parts which are not available. This will also eradicate any need for sending the parts to complex assembly lines to be finished.
In the aforementioned Aurora 3D printed aircraft, the ability to replace traditionally assembled parts into singular parts paves the way for intricate and complex design which improve performance significantly. Aurora’s jet benefits by this approach by 3D printing the fuel tank. The fuel tank now has 3D printed tubing, mounts that connect to the filter and fuel pump and small clamps to attach the fuel lines all in a single 3D printed part instead of being manufactured individually and assembled later. This design had the additional benefit of accurately handling the centre of gravity, a crucial parameter for blended wing aircraft.
Sustainability
Let’s examine the usual amount of wastage when using the subtractive method of manufacturing in the aviation industry. To make titanium aircraft components weighing about 300 pounds, the process is initiated with a 6000 pounds block of titanium. The block is then cut down and shaped into the required, precise form. This requires several gallons of coolant and about 5700 pounds of titanium chips that need to be recycled. Other processes have a similar wastage ratio.
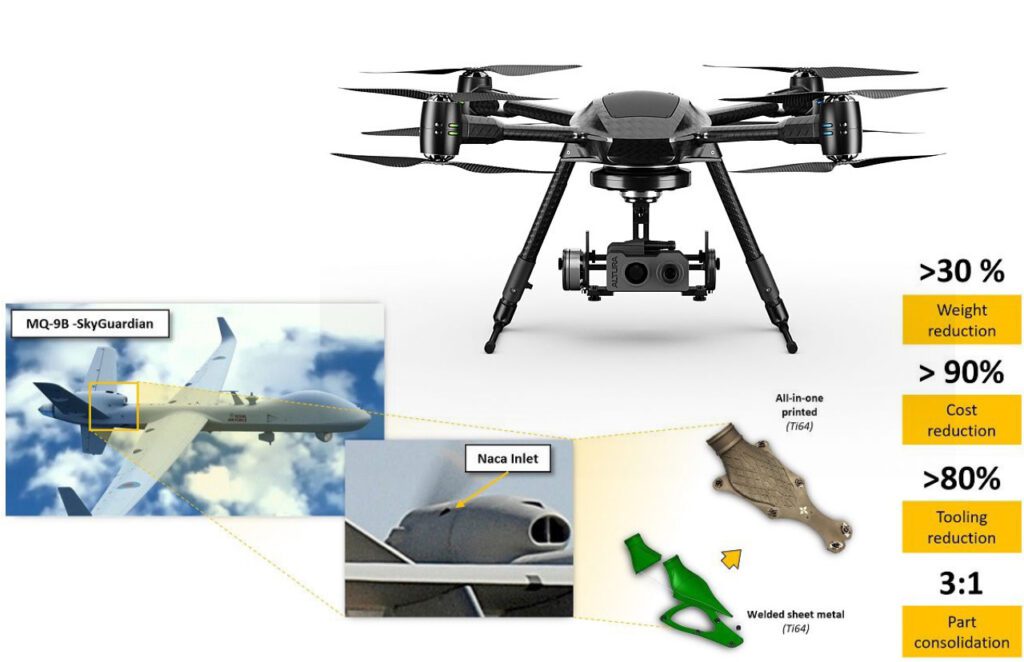
Fuel accounts for 30-50% of an aircraft’s operating cost. International Aviation Transport Authority (IATA) made a speculation in 2018 that aviation fuel cost will keep constantly increasing for the next decade. Higher fuel costs mean higher ticket pricing and vice versa.
Fortunately, additive manufacturing is inherently much more efficient. Autodesk, one of the leading CAD software developers, did a proof of concept for an Airbus seat. Using traditional casting and 3D printing processes, a prototype seat for economy class was created. This seat was 56% lighter than its current counterpart. If we look at the fuel consumed by an Airbus A380, replacing the currents seats with these will mean saving 63 tons of fuel per annum, which would mean 190.1 tons of less carbon emissions. This would be equal to taking 120,000 cars off the roads for an entire year. This is how 3D printing can make a significant difference.
Another aircraft that is in development, which also exhibits the sustainable factor, is the joint venture of Airbus and Local Motors Industries (LMI)from San Francisco. Titled Neorizon, the project includes manufacturing a ‘micro-factory’ which would hold the capability to build transportation vehicles like drones and automated cars using additive manufacturing. LMI already has experience in the area, with their self-driving shuttle named ‘Olli’, which was manufactured using 100% 3D printed parts. Neorizon is the next step for LMI. In the current model, cars and other vehicles are manufactured in specialised factories and then shipped to consumers. The idea of Neorizon is to shed this process and have micro-factories which would be erected where the actual demand is. These factories would then manufacture vehicles according to the actual demand, making the model more eco-friendly and sustainable than the traditional one.
According to Toyota, the average car has about 30,000 parts, which requires a huge supply network. 3D printing has the potential to change all of this, making it possible to spot-print parts for vehicles on demand, thus bypassing both the logistical supply problem and the problem of over- or under-stocking inventory.
Early Adapters
Owing to its obvious benefits, additive manufacturing is an area in which all aviation companies are willing to invest big. Aerospace constitutes up to 20% of the market share of additive printing and is growing rapidly. Major companies which are experimenting heavily with 3D printing, include:
Airbus
Airbus is already on its way to having a significant number of their aircraft parts being 3D printed. Some of their planes already have more than a hundred 3D printed parts, most of which weigh less than third of their former weight.
Boeing
Boeing has already acquired over 60, 000 parts using additive manufacturing. Boeing’s Dreamliner 737 uses 30 parts made using additive manufacturing and more are being developed.
Etihad
Etihad is scrutinizing its aircraft cabins, examining every part and estimating how much it would cost to 3D print them. Etihad’s innovation centre in Abu Dhabi is already working on redesigning non-flight parts and making them better and more efficient to manufacture. Its steps like these has led Etihad to be first airline to be MRO permitted by the EASA to manufacture, and utilise 3D printed parts.
Limitations of Additive Manufacturing
As is the case with all technologies in their infancies, additive manufacturing has its flaws and limitations too. It is not a panacea to overcome all obstacles. The different types each have their shortcomings and flaws, on which researchers are working. For example, it can be expensive, as compared to other methods. Another issue which usually arises is of poor surface finish and rough texture. This, in turn, leads to another shortcoming, the requirement of extensive post-post processing to get the desired results.
Another limitation of additive manufacturing is its current inability to be suitable for high volume manufacturing. Owing to its recent entry, its suppliers does not have widespread acceptability or access as compared to conventional suppliers that have worldwide presence. Factors like porosity is a problem. If you don’t entirely melt the tiny beads, you’re creating a porous material that will not have uniform properties. If those pores are close to the surface, you can create crack initiation sites, which can be a real problem with things such as aircraft wings. However, these problems are being resolved day by day and it is apparent to all that the importance of additive printing cannot be denied.
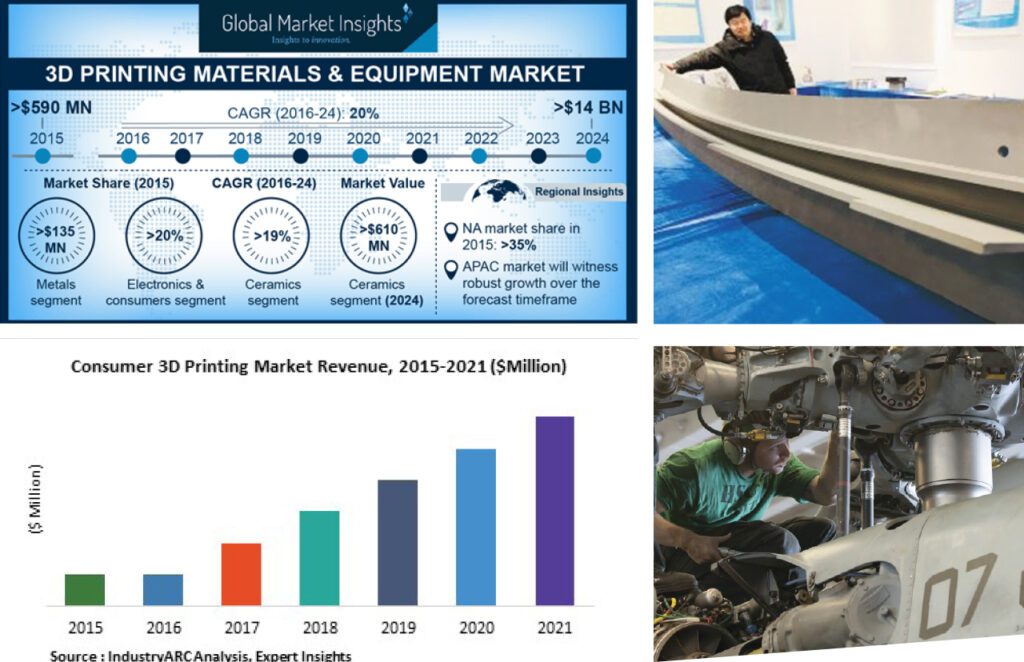
Additive printing is still in its infancy yet has already proven itself to be a gamechanger. With new players jumping into its advancement every single day, its only a matter of time before additive manufacturing becomes mainstream in all spheres of life.
Innovations are already underway. The Lawrence Livermore National Laboratory in California has 3D printers that can control metal fabrication on a microscopic level, creating alloys 3 times stronger than previous 3D metals. GE just unveiled a 3D printer which can manufacture a part more than a metre in length, which it uses to manufacture its new jet engine combustion liner. Supporters of the technology also predict that the method will mean significant advancements in space technology. The rocket manufacturer, ‘Relativity’, predicts that it will soon 3D print 95% of its satellite-carrying rockets.
With funds flowing in and interest soaring high, there is little doubt that 3D printed aircraft will one day fly freely in Earth’s sky and beyond.
References
Davies, A. (2019). 3D Printing Can Keep Aging Air Force Aircraft Flying. Retrieved May 2021, from wired.com: https://www.wired.com/story/air-force-3d-printing-parts-manufacturing-olympics/
General Electric. (2021). What is additive manufacturing? Retrieved May 2021, from GE Additive: https://www.ge.com/additive/additive-manufacturing
Kramer, J. (2019). 3D Printing Can Change The Aviation Industry. Retrieved May 2021, from blog.v-hr.com: https://blog.v-hr.com/blog/3d-printing-can-change-the-aviation-industry
McArthur, H. R. (2020). How 3D printing can, and cannot, change aviation forever. Retrieved 2021, from medium.com: https://medium.com/predict/how-3d-printing-can-and-cannot-change-aviation-forever-c8048201fd05